Како се машински обрађују делови високе прецизности
2023-09-22
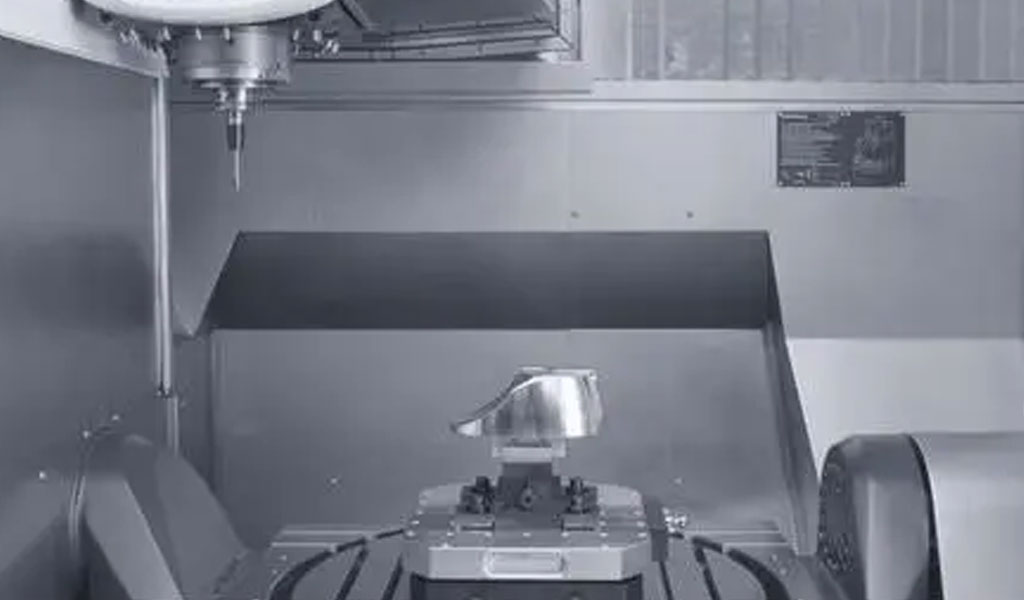
Разумевање прецизне обраде
Прецизна обрада је камен темељац модерне производње, одговоран за производњу сложених и тачних компоненти које се користе у широком спектру индустрија. Да бисмо у потпуности схватили њен значај, хајде да истражимо основне концепте прецизне машинске обраде, њену виталну улогу у различитим секторима и историјско путовање које је довело до њеног тренутног стања изврсности.А. Шта је прецизна обрада?
Прецизна обрада се односи на скуп производних процеса који уклањају материјал са радног комада са високим степеном тачности и контроле, што резултира фино израђеним компонентама са малим толеранцијама. Овај процес претвара сировине, као што су метали, пластика или керамика, у прецизне делове који испуњавају прецизне спецификације. Кључне карактеристике прецизне машинске обраде укључују:- Тачност: Прецизна обрада обезбеђује да се финални производ прецизно прилагоди предвиђеном дизајну, уз минимално одступање.
- Тигхт Толеранцес: Омогућава производњу делова са изузетно малим толеранцијама, што значи да се готове компоненте уско придржавају наведених мерења.
- Супериорна завршна обрада: Прецизна обрада обезбеђује изузетну завршну обраду површине, често елиминишући потребу за додатним процесима завршне обраде.
- Цомплек Геометри: Може да креира сложене облике, контуре и карактеристике, што га чини незаменљивим у производњи компоненти са сложеним дизајном.
- Поновљивост: Прецисион процес обрадеови су веома поновљиви, обезбеђујући конзистентан квалитет у више делова.
- Прилагодљивост: Може се применити на широк спектар материјала, што га чини погодним за различите индустрије.
Б. Важност прецизне обраде
Прецизна обрада има огроман значај у неколико критичних индустрија, утичући на различите аспекте нашег свакодневног живота. Ево неколико убедљивих разлога за његову важност:- Аероспаце Индустри: У сектору ваздухопловства, прецизна обрада је неопходна за израду компоненти које издржавају екстремне услове. Мотори авиона, слетање зупчаник, а структурни елементи се ослањају на прецизно обрађене делове за безбедност и перформансе.
- Медицински уређаји: Медицински уређаји као што су хируршки инструменти, протетика и имплантабилни уређаји захтевају прецизну машинску обраду ради биокомпатибилности, тачности и безбедности пацијената.
- Аутомотиве Сецтор: Прецизно обрађени делови су неопходни за аутомобилску индустрију како би се осигурала поузданост и ефикасност возила. Компоненте као што су делови мотора, системи преноса и кочиони механизми ослањају се на прецизну машинску обраду.
- Електроника и полупроводници: Прецизна обрада је кључна у производњи микроелектронских компоненти и полупроводничких уређаја, где су минималне толеранције императив за функционалност.
- Енергетски сектор: Енергетска индустрија се ослања на прецизну машинску обраду за производњу критичних делова који се користе у производњи електричне енергије, укључујући турбине, генераторе и компоненте за пренос.
- Израда алата и калупа: Прецизна обрада је кључна у производњи алата и калупа, који се, заузврат, користе за стварање безброј других производа.
- Електроника: Производња паметних телефона, лаптопова и друге потрошачке електронике има користи од прецизне машинске обраде како би се обезбедио елегантан дизајн и оптимална функционалност.
- Истраживање и развој: Истраживачи и научници зависе од прецизно обрађених компоненти за експерименте, прототипове и лабораторијску опрему.
Ц. Историјска перспектива
Путовање прецизне машинске обраде сеже до древних цивилизација, где су вешти занатлије користили рудиментарне алате за обликовање материјала. Међутим, прецизност постигнута у то време била је ограничена у поређењу са савременим стандардима.- Рана прецизна обрада: Индустријска револуција 18. и 19. века обележила је кључни период у развоју прецизне машинске обраде. Проналазак машина алатки, као што су стругови и глодалице, револуционирао је производњу омогућавајући већу тачност и конзистентност.
- Други светски рат: Прецизна обрада је играла кључну улогу у Другом светском рату, јер је била неопходна за производњу војне опреме са потребном прецизношћу и униформношћу. Ова ера је била сведок напретка у техникама машинске обраде и појаве нових материјала.
- Послератни напредак: У послератном периоду дошло је до пораста технолошких иновација, укључујући употребу компјутерских машина за нумеричко управљање (ЦНЦ). ЦНЦ обрада омогућавају аутоматизоване и веома прецизне операције, отварајући нову еру производње.
- Дигитално доба: Интеграција рачунара и софтвера у процесе обраде додатно је подигла прецизну машинску обраду. Модерне ЦНЦ машине могу да изврше сложене операције са неупоредивом прецизношћу, што их чини незаменљивим у данашњем производном окружењу.
Материјали и њихов значај
Материјали су основа прецизне машинске обраде, а избор правог материјала игра кључну улогу у производњи високо прецизних делова. У овом одељку ћемо се позабавити значајем одабира одговарајућих материјала, разумети значај својстава материјала и истражити различите факторе који утичу на обрадивост.А. Избор материјала
Избор материјала у прецизној машинској обради је критична одлука која директно утиче на перформансе, издржљивост и функционалност финалног производа. Произвођачи морају узети у обзир неколико фактора приликом одабира материјала:- Погодност материјала: Материјал мора бити погодан за предвиђену примену. Различите индустрије и примене имају различите захтеве, као што су отпорност на температуру, отпорност на корозију и електрична проводљивост.
- Механичка својства: Механичке особине као што су затезна чврстоћа, тврдоћа и дуктилност су кључне. На пример, у ваздухопловству, материјали са високом затезном чврстоћом су пожељнији за структурне компоненте.
- Термичка својства: Неке примене захтевају материјале са одличном топлотном проводљивошћу или отпорношћу на високе температуре. Ово је посебно важно у индустријама као што су производња електричне енергије и електроника.
- Отпорност на корозију: У окружењима где је корозија забрињавајућа, пожељни су материјали са високом отпорношћу на корозију, као што су нерђајући челик или титанијум.
- Разматрање тежине: Индустрије попут аутомобилске и ваздухопловне индустрије често дају предност лаким материјалима као што су алуминијум или композити од угљеничних влакана да би се смањила потрошња горива и побољшале перформансе.
- Ограничења трошкова: Цена је значајан фактор у избору материјала. Материјали високих перформанси могу бити скупи, тако да произвођачи морају успоставити равнотежу између перформанси и исплативости.
- Регулаторна Усклађеност: У индустријама као што је здравство, материјали морају да испуњавају строге регулаторне стандарде за биокомпатибилност и безбедност.
- Доступност: Доступност материјала и њихови извори такође утичу на избор. Неке специјализоване легуре или композити могу имати ограничену доступност.
Б. Својства материјала
Разумевање својстава материјала је кључно за прецизну машинску обраду. Ево неких кључних својстава материјала и њиховог значаја:- Затезна чврстоћа: Затезна чврстоћа мери способност материјала да издржи силу вуче без лома. Неопходан је за структурне компоненте и делове који су изложени механичком напрезању.
- Чврстоћа: Тврдоћа означава отпорност материјала на деформације и хабање. Тврди материјали су погодни за алате за сечење, док мекши материјали могу бити пожељнији за одређене примене, као што су заптивке.
- Дуктилност: Дуктилност се односи на способност материјала да се деформише без лома када је подвргнут затезном напрезању. Дуктилни материјали се лакше обликују, али можда нису погодни за апликације које захтевају крутост.
- Топлотна проводљивост: Материјали високе топлотне проводљивости ефикасно расипају топлоту. Ово својство је од виталног значаја у апликацијама где је контрола температуре критична.
- Електрична проводљивост: Електрична проводљивост је неопходна у електроници и електричним компонентама, где материјали морају да олакшају проток електричне енергије.
- Магнетиц Пропертиес: Магнетна својства су значајна у индустријама као што су електромагнетика и електроника, где ће материјали можда морати да буду феромагнетни или немагнетни.
- Хемијска отпорност: Материјали морају бити отпорни на хемијску корозију у срединама где су изложени киселинама, базама или другим корозивним супстанцама.
Ц. Фактори обрадивости
Обрадивост се односи на лакоћу са којом се материјал може машински обрађивати, сећи или обликовати. На то утичу различити фактори, укључујући:- Тврдоћа материјала: Мекши материјали се генерално лакше обрађују, док тврђи материјали могу захтевати специјализоване алате и технике.
- Формирање чипова: Формирање и евакуација струготине током обраде утиче на ефикасност процеса и завршну обраду површине.
- Тоол Веар: Различити материјали могу изазвати различите степене хабања алата, утичући на брзину обраде и цену.
- Расхладна течност и подмазивање: Правилно расхладно средство и подмазивање су од суштинског значаја за смањење трења, топлоте и хабања алата током обраде.
- Брзина сечења: Брзина којом се резни алат креће кроз материјал утиче и на продуктивност и на квалитет обрађене површине.
- Материјал алата: Избор материјала резног алата, као што је карбид или брзорезни челик, зависи од материјала који се обрађује.
- Параметри сечења: Подешавање параметара сечења као што су брзина помака и дубина резања може оптимизовати процес обраде за одређене материјале.
Машине алатке за прецизну машинску обраду
Машине алатке су срце прецизне машинске обраде, омогућавајући трансформацију сировина у делове високе прецизности. У овом одељку ћемо истражити четири кључна типа машина алатки које се користе у прецизној машинској обради: ЦНЦ обрадни центри, машине за стругање, машине за брушење и ЕДМ (електрична обрада). Свака од ових машина игра јединствену улогу у производњи прецизних компоненти.А. ЦНЦ обрадни центри
ЦНЦ (компјутерска нумеричка контрола) обрадни центри су разноврсни и широко се користе у прецизној машинској обради. То су аутоматизовани системи који контролишу кретање резних алата и радних предмета са изузетном прецизношћу. Ево прегледа ЦНЦ обрадних центара и њиховог значаја:- Прилагодљивост: ЦНЦ обрадни центри могу да изводе различите операције обраде, укључујући глодање, бушење и урезивање. Ова свестраност омогућава производњу сложених делова са више функција.
- Високу прецизност: Компјутеризована контрола ЦНЦ машина обезбеђује прецизно позиционирање алата и доследне резултате, што их чини идеалним за делове са малим толеранцијама.
- Аутоматизација: ЦНЦ обрадни центри могу да раде континуирано, уз минималну људску интервенцију. Ова аутоматизација повећава ефикасност и смањује ризик од грешака.
- Цомплек Геометри: Они се истичу у машинској обради сложених облика и контура, што их чини погодним за индустрије попут ваздухопловства, где су сложене компоненте уобичајене.
- Поновљиви резултати: ЦНЦ машине нуде одличну поновљивост, обезбеђујући да сваки произведени део одговара тачним спецификацијама дизајна.
- Смањено време подешавања: ЦНЦ обрадни центри се могу програмирати да брзо прелазе између различитих задатака, минимизирајући време подешавања и повећавајући ефикасност производње.
Б. Стројеви за стругање
Машине за стругање се користе за стварање цилиндричних делова ротацијом радног предмета док алат за сечење уклања материјал са његове спољне површине. Они су неопходни за производњу вратилос, игле и друге компоненте са ротационом симетријом. Кључне тачке о машинама за окретање укључују:- Цилиндрични делови: Машине за стругање специјализоване су за производњу цилиндричних или цевастих компоненти, укључујући оне са навојем или замршеним жлебовима.
- Хигх Спеедс: Раде при великим брзинама, што их чини погодним за делове који захтевају глатку и прецизну завршну обраду.
- Једноосни рад: Већина машина за стругање је једноосна, фокусирајући се на обликовање спољашње површине радног предмета.
- Ефикасан за масовну производњу: Стругање је веома ефикасно за делове масовне производње са минималним отпадом материјала.
- Токарске машине: Ручне и ЦНЦ-контролисане стругове машине су обично коришћене машине за стругање, нудећи низ могућности.
Ц. Машине за млевење
Машине за брушење су дизајниране за прецизну завршну обраду и обликовање тврдих или абразивних материјала. Они су кључни за постизање изузетно чврстих толеранција и врхунске завршне обраде површине. Ево зашто су машине за млевење важне:- Прецизност на нивоу микрона: Машине за брушење могу постићи прецизност на нивоу микрона, што их чини неопходним за апликације које захтевају највиши ниво тачности.
- Уклањање материјала: Одстрањују материјал абразијом, омогућавајући корекцију несавршености површине и постизање изузетне глаткоће.
- Брушење алата и резача: Поред површинског брушења, постоје специјализоване машине за брушење за оштрење резних алата и израду прецизних профила.
- Разноликост метода млевења: Различити типови машина за брушење, укључујући површинске брусилице, цилиндричне брусилице и брусилице без центра, задовољавају различите потребе обраде.
- Харденед Материалс: Брушење је посебно погодно за каљене материјале као што су алатни челик и керамика, где традиционалне методе обраде могу бити неефикасне.
Д. ЕДМ (електрична обрада)
ЕДМ, или обрада са електричним пражњењем, је нетрадиционални процес обраде који користи електрична пражњења за обликовање материјала. Идеалан је за стварање замршених и деликатних делова где традиционални алати за сечење могу да изазову штету. Кључни аспекти ЕДМ-а укључују:- Нема физичког контакта: ЕДМ не укључује директан физички контакт између алата и радног предмета, минимизирајући ризик од хабања алата и оштећења ломљивих материјала.
- Високу прецизност: Може постићи високу прецизност и квалитет површине, чак и са изузетно тврдим материјалима.
- Вире ЕДМ и Синкер ЕДМ: Постоје две основне врсте ЕДМ машина: сечење жице ЕДМ, који користи жичану електроду, и синкер ЕДМ, који користи обликовану електроду.
- Цомплек Схапес: ЕДМ може да произведе сложене облике, као што су калупи и калупи, са сложеним детаљима и финим карактеристикама.
- Зона погођена топлотом: Пошто ЕДМ не ствара топлоту на радном предмету, погодан је за материјале осетљиве на топлоту као што су легуре за ваздухопловство.
- Споро процес: ЕДМ је релативно спор у поређењу са другим методама обраде, што га чини најпогоднијим за послове мале количине, високе прецизности.
Алати за сечење и алати
Алати за сечење су на челу прецизне машинске обраде, служећи као инструменти који обликују и трансформишу сировине у делове високе прецизности. У овом одељку ћемо истражити различите врсте алата за сечење, важност премаза алата и факторе који утичу на век трајања и хабање алата.А. Врсте алата за сечење
Прецизна обрада се ослања на разноврсне алате за сечење, од којих је сваки дизајниран за специфичне задатке и материјале. Избор алата за сечење у великој мери утиче на ефикасност и тачност процеса обраде. Ево неких уобичајених типова алата за сечење:- Енд Миллс: Завршне глодалице су свестрани алати који се користе за операције глодања. Имају више резних ивица и могу да уклоне материјал са радног предмета на различите начине, укључујући облагање, обликовање и урезивање.
- Бушилице: Бушилице су дизајниране за прављење рупа у радним комадима. Долазе у различитим облицима, укључујући спиралне бушилице, централне бушилице и бушилице које се могу индексирати.
- Турнинг Инсертс: Користе се у машинама за стругање за обликовање цилиндричних делова. Уметци за окретање су доступни у различитим облицима и материјалима који одговарају различитим применама.
- Миллинг Цуттерс: Глодалице долазе у различитим облицима, као што су чеони глодали, куглични млинови и глодалице за урезивање, и користе се у машинама за глодање за креирање различитих карактеристика на радном комаду.
- Развртачи: Развртачи се користе за завршну обраду и димензионисање претходно избушених рупа до прецизних димензија. Они обезбеђују глатке и прецизне површине рупа.
- Тапс анд Диес: Ови алати за сечење се користе за операције урезивања навоја. Славине стварају унутрашње навоје, док матрице стварају спољашње навоје.
- Брусни точкићи: Брусни точкови су абразивни алати који се користе за прецизно брушење површине. Доступни су у различитим абразивним материјалима и величинама зрна.
- Брошеви: Броашеви су специјализовани алати који се користе за сечење унутрашњих и спољашњих облика и профила, као што су утори за кључеве и клинови.
- Протуци и упуштачи: Ови алати се користе за прављење удубљења или ивица око рупа за затварачs.
- Боринг Барс: Шипке за бушење се користе у операцијама бушења за повећање постојећих рупа са прецизношћу.
Б. Премази алата
Премази алата су танки слојеви материјала који се наносе на резне алате како би се побољшале њихове перформансе и издржљивост. Ови премази нуде неколико предности:- Редуцед Фрицтион: Премази попут титанијум нитрида (ТиН) и титанијум карбонитрида (ТиЦН) смањују трење између алата и радног предмета, што доводи до глатког сечења и дужег века алата.
- Енханцед Харднесс: Премази повећавају тврдоћу површине алата, чинећи га отпорнијим на хабање и продужавајући век трајања алата.
- Побољшана отпорност на топлоту: Премази могу да издрже високе температуре настале током обраде, смањујући хабање алата повезано са топлотом и повећавајући брзину резања.
- Својства против накупљања: Неки премази имају својства против приањања, спречавајући накупљање материјала на резним ивицама алата.
- Повећана мазивост: Алати са премазом имају побољшану способност подмазивања, смањујући потребу за прекомерном расхладном течношћу и побољшавајући евакуацију струготине.
Ц. Животни век и хабање алата
Разумевање века трајања алата и хабања је кључно за оптимизацију процеса обраде и минимизирање трошкова производње. Век трајања алата се односи на време трајања алата за сечење пре него што га треба заменити или поправити. Неколико фактора утиче на век трајања и хабање алата:- Брзина сечења: Веће брзине резања могу довести до повећаног хабања алата због виших температура које настају током обраде. Правилан избор брзина резања је од суштинског значаја за балансирање века алата и продуктивности.
- Феед Рате: Брзина којом резни алат напредује у радни предмет утиче на хабање алата. Високе брзине помака могу убрзати хабање, док ниже брзине помака могу продужити век трајања алата.
- Дубина реза: Дубина сечења утиче на количину уклоњеног материјала по пролазу. Дубљи резови могу повећати хабање алата, тако да је оптимизација дубине критична.
- Тврдоћа материјала: Резање тврдих материјала може убрзати хабање алата. За ефикасну обраду тврдих материјала користе се специјализовани алати и премази.
- Расхладна течност и подмазивање: Одговарајућа течност за хлађење и подмазивање помажу у расипању топлоте и смањењу трења, продужавајући век трајања алата.
- Материјал алата: Материјал од којег је направљен резни алат утиче на његову отпорност на хабање. Материјали попут карбида и керамике нуде одличну отпорност на хабање.
- Геометрија алата: Геометрија алата за сечење, укључујући нагибни угао, угао рељефа и дизајн ломача струготине, игра значајну улогу у обрасцима хабања.
- Материјал радног предмета: Врста материјала који се обрађује утиче на хабање алата. Абразивни материјали могу довести до бржег хабања алата.
Прецизни процеси обраде
Прецизни процеси машинске обраде су методе помоћу којих се сировине претварају у високо прецизне делове са малим толеранцијама и изузетним завршним обрадама површине. У овом одељку ћемо истражити пет кључних процеса прецизне обраде: стругање, глодање, бушење, брушење и обрада са електричним пражњењем (ЕДМ). Сваки од ових процеса служи јединственој сврси и користи се на основу специфичних захтева радног комада.А. Окретање
Токарење је процес машинске обраде који се првенствено користи за обликовање цилиндричних делова. Укључује ротацију радног предмета док алат за сечење у једној тачки уклања материјал са спољне површине. Ево кључних аспеката окретања:- Цилиндрични делови: Токарење је идеално за производњу цилиндричних компоненти као што су осовине, игле и чауре.
- Ротациона симетрија: Погодан је за делове који захтевају ротациону симетрију, пошто се радни предмет ротира на стругу док га резни алат обликује.
- Разне операције: Токарење може обављати различите операције, укључујући облагање, окретање (смањење пречника), конусно окретање и урезивање навоја.
- Сечење у једној тачки: Један алат за сечење уклања материјал у непрекидном кретању, што резултира ефикасним уклањањем материјала.
- Токарске машине: И ручне и ЦНЦ-контролисане стругове машине се обично користе за операције стругања.
Б. Глодање
Глодање је свестран прецизан процес обраде који користи алате за сечење са више тачака за уклањање материјала са радног комада. Погодан је за креирање широког спектра облика и карактеристика. Кључни аспекти млевења укључују:- Прилагодљивост: Глодање може произвести равне површине, уторе, џепове и сложене контуре. Користи се и за 2Д и 3Д машинску обраду.
- Сечење у више тачака: Више резних ивица на алату истовремено комуницира са радним предметом, омогућавајући ефикасно уклањање материјала.
- Врсте глодања: Глодање се може изводити помоћу различитих типова глодала, укључујући крајње глодалице, чеоне глодалице и кугличне млинове.
- ЦНЦ обрадни центри: ЦНЦ контролисане глодалице нуде прецизну контролу кретања алата и широко се користе у модерној машинској обради.
- Хигх Спеедс: Глодање се може изводити при великим брзинама, што омогућава ефикасну производњу.
Ц. Бушење
Бушење је прецизан процес обраде који се користи за стварање рупа у радним комадима. То је основна операција у различитим индустријама. Кључни аспекти бушења укључују:- Креирање рупа: Машине за бушење користе специјализоване алате зване бушилице за уклањање материјала и стварање рупа одређених пречника.
- Врсте бушилица: Доступне су различите врсте бушилица, укључујући спиралне бургије, централне бушилице и бушилице које се могу индексирати, свака дизајнирана за специфичне примене.
- Тачност: Прецизно позиционирање и поравнање су од суштинског значаја за бушење како би се обезбедило да се рупе праве са прецизношћу.
- Брзина и брзина увлачења: Параметри бушења као што су брзина ротације и брзина помака су критични за постизање жељених димензија рупе.
- Расхладна течност и подмазивање: Одговарајућа течност за хлађење и подмазивање се користе за одвођење топлоте и смањење трења током бушења.
Д. Брушење
Брушење је прецизан процес обраде који користи абразивне точкове за уклањање материјала и постизање изузетно чврстих толеранција и завршне обраде површине. Кључни аспекти млевења укључују:- Изузетна прецизност: Брушење може постићи прецизност на нивоу микрона, што га чини идеалним за апликације које захтевају највећу прецизност.
- Завршно: Производи врхунске завршне обраде површине, често елиминишући потребу за додатним процесима завршне обраде.
- Materijali: Брушење је погодно за тврде и абразивне материјале, укључујући каљени челик, керамику и карбиде.
- Разноликост метода млевења: Различите врсте машина за брушење, као што су брусилице за површине, цилиндричне брусилице и брусилице без центра, задовољавају различите потребе машинске обраде.
- Расхладна течност: Одговарајућа расхладна течност је неопходна за брушење како би се спречило прегревање и одржао интегритет точка.
Е. Машинска обрада са електричним пражњењем (ЕДМ)
ЕДМ, или обрада са електричним пражњењем, је нетрадиционални прецизан процес обраде који користи електрична пражњења за уклањање материјала. Посебно је погодан за обраду сложених и замршених облика, као и тврдих материјала отпорних на топлоту. Кључни аспекти ЕДМ-а укључују:- Бесконтактна обрада: ЕДМ не укључује директан контакт између алата и радног комада, смањујући ризик од хабања и оштећења алата.
- Високу прецизност: ЕДМ може постићи високу прецизност, што га чини погодним за апликације где су чврсте толеранције неопходне.
- Цомплек Схапес: Одликује се у обради сложених облика, калупа, калупа и компоненти са финим детаљима.
- Вире ЕДМ и Синкер ЕДМ: Постоје два примарна типа ЕДМ машина: жичана ЕДМ, која користи жичану електроду, и ЕДМ са потопом, која користи обликовану електроду.
- Споро процес: ЕДМ је релативно спор у поређењу са другим методама обраде, што га чини најпогоднијим за послове мале количине, високе прецизности.
Толеранције и контрола квалитета
Прецизна обрада захтева пажљиву пажњу на детаље и ригорозну посвећеност контроли квалитета како би се осигурало да делови испуњавају наведене стандарде. У овом одељку ћемо истражити три критична аспекта контроле квалитета у прецизној машинској обради: геометријско димензионисање и толеранцију (ГД&Т), статистичку контролу процеса (СПЦ) и осигурање квалитета.А. Геометријско димензионисање и толеранција (ГД&Т)
Геометријско димензионисање и толеранција, често скраћено ГД&Т, је систем који се користи за дефинисање и саопштавање дозвољених варијација у величини, облику, оријентацији и локацији карактеристика на делу. ГД&Т је од виталног значаја у прецизној машинској обради из следећих разлога:- Прецисе Цоммуницатион: ГД&Т обезбеђује стандардизовани језик за инжењере, дизајнере и машинисте да прецизно пренесу намеру дизајна и захтеве димензија.
- Појашњење толеранције: Помаже у дефинисању прихватљивих варијација у критичним димензијама, осигуравајући да све заинтересоване стране разумеју дозвољена одступања.
- Унапређен квалитет: ГД&Т промовише побољшани квалитет смањујући двосмисленост у спецификацијама дизајна, минимизирајући ризик од грешака током обраде.
- Ефикасност трошка: Јасне ГД&Т спецификације могу довести до смањења трошкова производње, јер је мања вероватноћа да ће делови бити расходовани или захтевати дораду због неспоразума или погрешног тумачења.
- Цомплек Геометри: Посебно је користан за делове са сложеном геометријом, осигуравајући да су све карактеристике произведене према жељеним спецификацијама.
Б. Статистичка контрола процеса (СПЦ)
Статистичка контрола процеса (СПЦ) је методологија контроле квалитета која користи статистичке технике за праћење и контролу процеса обраде. СПЦ је неопходан у прецизној машинској обради из следећих разлога:- Надгледање процеса: СПЦ помаже у праћењу процеса обраде у реалном времену, идентификујући варијације или одступања од жељених параметара.
- Рано откривање проблема: Континуираним праћењем процеса, СПЦ омогућава рано откривање проблема који би могли да доведу до делова ван спецификације, смањења отпада и прераде.
- Доношење одлука засновано на подацима: СПЦ се ослања на податке и статистичку анализу да би донео информисане одлуке о прилагођавању процеса, обезбеђујући да процес обраде остане у прихватљивим границама.
- Побољшана конзистентност: СПЦ промовише доследност процеса и смањује вероватноћу производње неусаглашених делова.
- Смањени отпад и прерада: Благовременим идентификовањем и адресирањем варијација процеса, СПЦ минимизира производњу неисправних делова, смањујући трошкове отпада и прераде.
Ц. Осигурање квалитета прецизне обраде
Осигурање квалитета у прецизној машинској обради обухвата свеобухватан приступ осигуравању да произведени делови испуњавају или премашују одређене стандарде квалитета. Укључује различите елементе, укључујући:- Процесна документација: Детаљна документација процеса обраде, укључујући стандардне радне процедуре (СОП) и упутства за рад, осигурава да се сваки корак изводи доследно.
- Инспекција и мерење: Ригорозна инспекција и мерење коришћењем прецизних инструмената и метролошких техника потврђује да су делови усклађени са одређеним толеранцијама и стандардима квалитета.
- калибрисање: Редовна калибрација опреме за машинску обраду и мерних инструмената је неопходна за одржавање тачности и следљивости.
- Верификација материјала: Провера својстава материјала, састава и квалитета је критична да би се осигурало да коришћени материјал испуњава захтеве дизајна.
- Обука запослених: Програми обуке и развоја вештина за машинисте и особље за контролу квалитета обезбеђују да они буду вешти у својим улогама и одговорностима.
- Анализа узрока узрока: Када се идентификују неусаглашени делови, спроводи се анализа основног узрока како би се утврдио извор проблема и спровеле корективне мере.
- Континуирано унапређење: Култура сталног побољшања подстиче иновације и покреће стална побољшања у процесима обраде и процедурама контроле квалитета.
- Кориснички Феедбацк: Прикупљање и анализа повратних информација купаца помаже у идентификацији области за побољшање и усклађује процесе обраде са очекивањима купаца.
Zakljucak
А. Уметност и наука прецизне обраде
Прецизна обрада је на раскрсници уметности и науке, где се креативност, вештина и иновација спајају да би произвели делове високе прецизности који покрећу индустрију и обликују савремени свет. То је и облик уметности, који захтева занатско умеће и стручност машиниста који претварају сировине у дела инжењерске изврсности, и наука која се ослања на најсавременију технологију, науку о материјалима и напредне процесе како би се постигла неупоредива прецизност. Путовање прецизне машинске обраде води нас кроз разумевање материјала и њихових особина, савладавање алата и машина за сечење, као и прецизну контролу процеса и толеранција. Обухвата језик геометријског димензионисања и толеранције, будност статистичке контроле процеса и посвећеност обезбеђивању квалитета. Прецизна обрада игра кључну улогу у различитим индустријама, од ваздухопловства и аутомобила до медицинских уређаја и електронике, обликујући све, од мотора авиона до вештачких зглобова и микрочипова. Омогућава креирање компоненти које раде са неупоредивом тачношћу и поузданошћу, често померајући границе могућег.Б. Завршне мисли
Како закључујемо ово истраживање прецизне машинске обраде, јасно је да се у овој области не ради само о стварању делова; ради се о стварању могућности. Потрага за прецизношћу покреће иновације, померајући границе онога што се може постићи. Било да се ради о деликатној изради која је потребна за креирање сложених зупчаника сата или о напредној технологији потребној за производњу сложених ваздухопловних компоненти, прецизна обрада је у срцу свега. Будућност прецизне машинске обраде пуна је обећања. Напредак у науци о материјалима, аутоматизацији и дигиталним технологијама наставља да преобликује пејзаж. Минијатуризација, 3Д штампање и праксе одрживе производње постају све истакнутије, отварајући нове хоризонте за индустрију. У свету где је прецизност важнија него икад, прецизна обрада остаје незаменљив стуб модерног инжењерства. То је сведочанство људске генијалности и наше непопустљиве тежње за изврсношћу у сваком аспекту производње. Како потражња за вишом прецизношћу и сложенијим компонентама расте, прецизна обрада ће наставити да се развија, суочавајући се са изазовима сутрашњице са истом посвећеношћу и прецизношћу која је дефинисала вековима.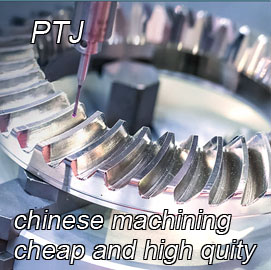
Naše usluge
- 5 осна обрада
- Цнц глодање
- ЦНЦ окретање
- Машинска индустрија
- Процес обраде
- Површинска обрада
- Машинска обрада метала
- Обрада пластике
- Калуп за металургију праха
- Дие Цастинг
- Галерија делова
Klijenti
- Ауто метални делови
- Машински делови
- ЛЕД хладњак
- Буилдинг Партс
- Мобилни делови
- Медицински делови
- Електронски делови
- Прилагођена обрада
- делови за бицикл
Листа материјала
- Машинска обрада алуминијума
- Обрада титана
- Обрада нерђајућег челика
- Машинска обрада бакра
- Обрада месинга
- Обрада супер легура
- Пеек Мацхининг
- УХМВ Мацхининг
- Унилате Мацхининг
- ПА6 Обрада
- ППС Мацхининг
- Тефлонска обрада
- Инцонел Мацхининг
- Обрада челичног алата
- Више материјала
Галерија делова